CNC WATERJET CUTTING
Cutting Experts is a leading provider of high-quality water jet cutting services for materials ranging from industrial plastics such as UHMW, HDPE, Starboard, Delrin, polypropylene, ABS, Teflon, Polycarbonate, acrylic, PVC and other abrasive resistant plastics, to aluminum, stainless steel, specialty rubber or foam. This service is provided specifically for thru-cutting of those sheet type materials.
Our experienced team works across several inhouse machines to create close tolerance, distortion-free parts with superior edge quality, no burrs, and little need for secondary finishing.
Our organized workflow allows large waterjet jobs to stay on track and small jobs to flow quickly through the schedule. Over the years we have processed tens of thousands of CNC jobs. The range from prototypes to small batch orders to larger production orders. Our scale and organizational workflow allow us to supply customers with efficient and dependable lead times.
Utilizing advanced part nesting techniques and technology enables us to minimize material waste. We then pass that cost savings on to our customers in the quoting process.
Our high speed 2-axis equipment is able to generate up to 60,000 psi to cut through material up to 5″ thick at speeds up to 600″/minute. Able to create complex shapes and intricate patterns, we fabricate parts measuring up to 144″ x 77″ at tolerances to ± 003″, which is verified by NIST certified measuring equipment.
Ensuring customer satisfaction is a critical part of our operation. When you call Cutting Experts, you will be greeted by a member of our professional staff, not an automated answering system. We will even pick up raw material from your location in the North Georgia area and deliver the finished parts, at no additional charge to you. We will work with your CAD files, or digitally duplicate the part if a drawing is not available. In quantities from prototype to full production runs, we offer fast turnaround and very reasonable prices.
MATERIALS |
METALStainless Steel, Specialty Alloys and Aluminum
|
FOAMXLPE Foam, Closed Cell Neoprene Foam, EPDM Foam, PE Foam
|
RUBBEREPDM (Ethylene Propylene Diene), Butyl (IIR), Gum, Neoprene (CR), Nitrile (NBR), Silicone (SBR), Fluroelastomer (FKM)
|

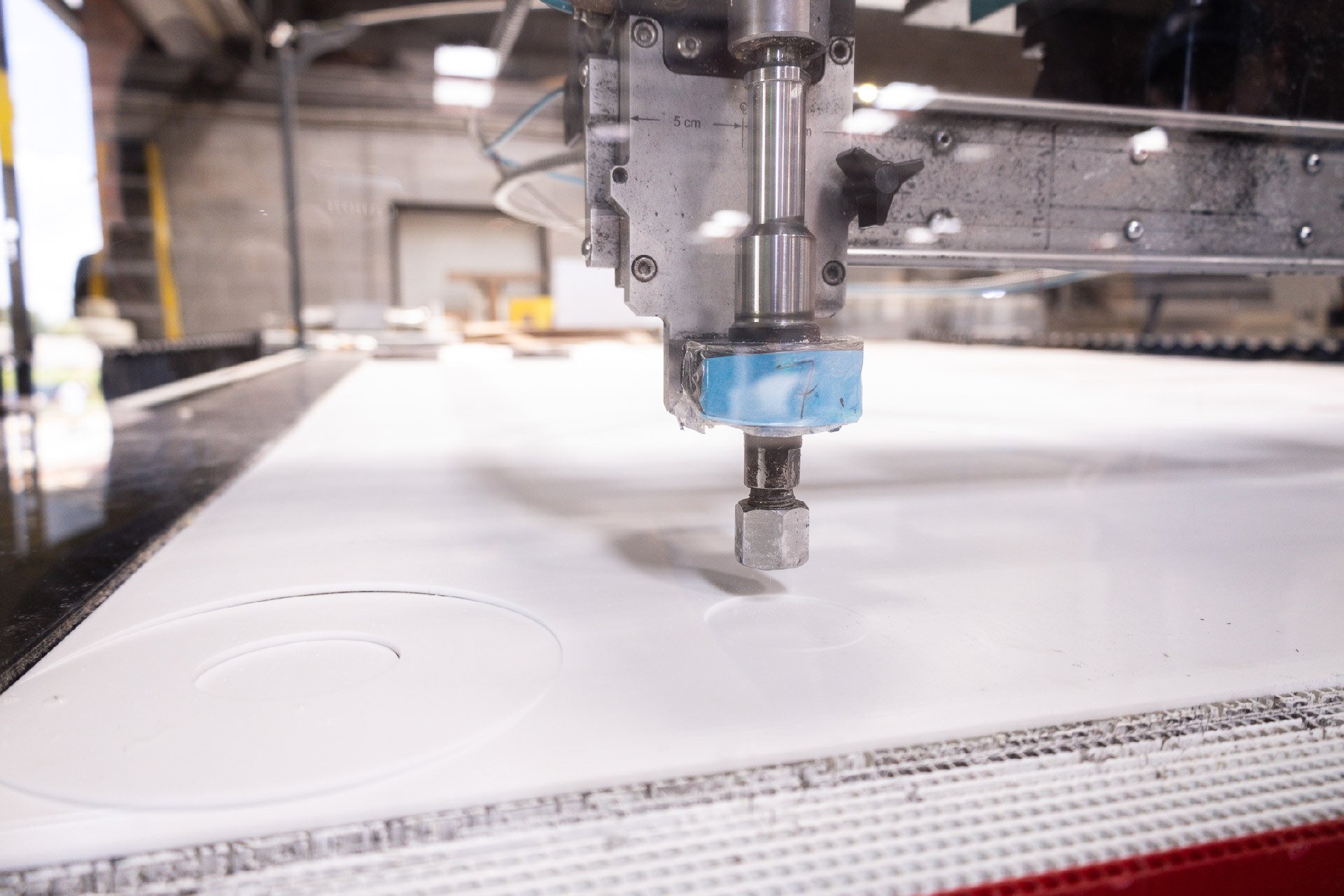
CHARACTERISTICS |
PROCESS |
|
Removes Taper Minimum Part Stress No Thermal Distortion or Hardening Reduced Material Cost Through Nesting Reduction or Elimination of Secondary Operations Smooth Finished Edges |
Water Abrasive |
|
CUTTING AXIS |
CUTTING THICKNESS |
|
Multi-Axis | Up to 5 inches | |
CUTTING LENGTH |
CUTTING WIDTH |
|
Up to 144 inches | Up to 77 inches | |
WATERJET PRESSURE |
CUTTING SPEED |
|
60,000 psi | Up to 600 in/min | |
KERF |
TOLERANCE |
|
.005 to .040 inches | Up to .003 in Depending on material and design |